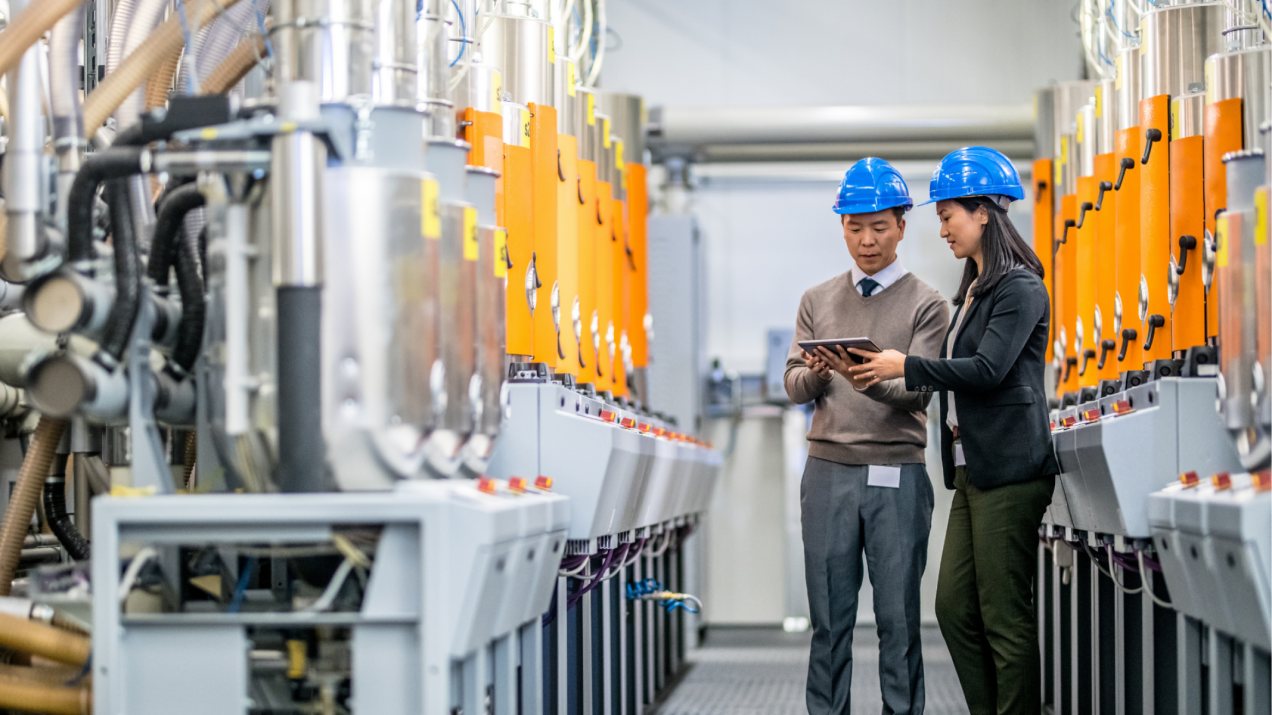
Another day, another breakdown in the factory. One of your actuators has broken down causing a 5-hour factory-wide downtime. You fix the actuator but the worst part is not the million(s) of lost revenue – the worst part is that you don’t know the reason why it happened and how to avoid that in the future. Doesn’t sound too good, right?
Now, imagine another scenario: you are operating your plant and one of your pumps is about to break down. However, before that happens, you are notified that this specific pump is nearing its useful life and are given predictions on how much longer can you operate the asset. Is that possible? Yes. How is the solution called? Asset Performance Management.
What is Asset Performance Management?
Asset Performance Management (or APM) is the practice of optimising the usage of company’s physical assets. That is achieved by combining the asset data collection, integration, visualisation, analytics and interpretation. Industrial organisations mainly benefit from Asset Performance Management solutions by improved product offering, decreased asset downtime, increased asset availability and lower maintenance costs.
Asset Performance Management is one of the foundational concepts of digital transformation. It is a combination of information sharing and application integration within maintenance and operations in order to provide an extensive view of asset performance, product quality and production. More specifically, Asset Performance Management focuses on the integration of production management and asset maintenance management.
Categorising Asset Performance Management
The broad notion of Asset Performance Management can be categorised into maintenance objectives, production objectives and the critical issues that must be avoided.
The objectives of asset availability, longevity, reliability and maintenance cost result in optimising the asset maintenance. Such maintenance objectives feed into the production objectives of on-time delivery, satisfactory quantity & quality levels and production cost. By optimising the processes of maintenance and production, the organisation is better equipped to deal with the critical process-related issues of sustainability, safety, operating constraints and energy.
Thus, it is clear that Asset Performance Management is an overarching system that requires a clear strategic direction from the company side in order to reap the full benefits.
Levels of Maintenance
As described previously, a large part of Asset Performance Management comes down to the asset maintenance optimisation. The different levels of maintenance can be categorised into 5 levels from the most manual to the most sophisticated in the maturity matrix adapted to APM.
Level 1 – Visual inspections
Maintenance is carried out periodically or according to a specified criteria in order to reduce the failure risk or performance degradation of the equipment. The main method of ensuring that assets are in satisfactory shape is visual (human) inspections.Thus, it is clear that APM is an overarching system that requires a clear strategic direction from the company side in order to reap the full benefits.
Level 2 – Instrument inspections
Maintenance is carried out periodically. The combination of visual and instrument inspections is used for making conclusions.
Level 3 – Real-time condition monitoring
Maintenance is carried out based on real-time equipment performance monitoring and corrective actions taken as a response. Maintenance is conducted when certain factors indicate the degradation of the equipment which increases the risk of failure. In the long-term, this strategy dramatically decreases the maintenance costs by reducing the occurrence of serious faults and optimising the asset performance.
Level 4 – Predictive maintenance (PdM)
Predictive maintenance is performed using condition-monitoring tools together with external data (e.g. environmental, historical data). AI-based predictive maintenance techniques are then used to predict the failure of assets using the integrated data and provide alerts. By operating assets in a more predictable fashion, the equipment downtime is minimised and asset lifetime is maximised. Predictive maintenance is especially suitable for managing critical operational functions where potential faults are detrimental.
Level 5 – Prescriptive maintenance (RxM)
Prescriptive maintenance is a concept that takes predictive maintenance a step further. Prescriptive maintenance is able to derive specific recommendations on how to further operate the deteriorating assets while also measuring the impact of the recommended solutions on the affected operations.
Final level – Digital twin
There is actually a final level that is not even defined in the Asset Performance Management Maturity Matrix. The concept of digital twin is a digital representation of a physical object or system. The idea behind the technology of the digital twin is creating the ability to manipulate physical assets or systems digitally in order to optimise their performance and make their outcomes as deterministic as possible.
This level of maintenance is still in its very early stage of adoption.
Benefits: Various Use Cases
With the advent of Industrial Internet of Things (IIoT) and Industry 4.0, different industrial organisations have different needs that can be fulfilled by a comprehensive integration of the Asset Performance Maintenance system.
The objectives of asset availability, longevity, reliability and maintenance cost result in optimising the asset maintenance. Such maintenance objectives feed into the production objectives of on-time delivery, satisfactory quantity & quality levels and production cost. By optimising the processes of maintenance and production, the organisation is better equipped to deal with the critical process-related issues of sustainability, safety, operating constraints and energy.
Thus, it is clear that Asset Performance Management is an overarching system that requires a clear strategic direction from the company side in order to reap the full benefits.
Machine Builders
Asset Performance Management solutions are especially compelling to the Machine Builders (or OEMs; Original Equipment Manufacturers) in this time when the product differentiation in manufacturing is increasingly more difficult to achieve. And one of the best ways to differentiate the product has become a layer of data analytics on top of the product stack. IIoT-enabled sensors coupled with predictive maintenance and prescriptive maintenance software enable the Machine Builders to offer data-driven products to their customers. Such offering expands company’s business model into aftermarket services for higher quality and reliability.
This switch to data-driven product manufacturing is advantageous as aftermarket services tend to have higher profit margins than the operating part of the business. The data analytics layer would be able to provide specific insights on asset usage and maximise the asset performance, minimise the downtime and improve the safety of the production facility. According to a report from McKinsey Global Institute, predictive maintenance and prescriptive maintenance can help OEMs decrease their costs by 10-40% by 2025 through operations optimisation.
Industrial Companies
Industrial Companies are mostly able to benefit from Asset Performance Management solutions by improving their maintenance practices and significantly reducing the maintenance costs. This is achieved by improving asset reliability and availability with predictive maintenance and prescriptive maintenance. Such improvements also help prevent the companies from experiencing asset failure, which leads to very expensive downtime.
A study by Aberdeen Group in 2016 found that the average costs of downtime across all businesses were $260,000 per hour and growing at a rapid pace of 26% per year compared to 2014. Combine that with an estimated 300 yearly downtime hours in the machinery & equipment industry and the total costs add up very quickly.
Maintenance Providers
Asset Performance Management solutions have the ability to transform the industry of Maintenance Providers (or MROs; Maintenance, Repair & Overhaul). A successful implementation of the APM practices in the company’s operations increases the quality of the maintenance provided while decreasing their operational costs. Such changes allow the Maintenance Providers to gain a significant competitive advantage if they switch to operating using performance-based rather than fixed contracts.
On top of that, the Maintenance Providers are able to maintain asset control, meaning constant surveillance of the assets they are responsible for. This, once again, enhances the company’s value offering. The maintenance market dynamics are rapidly changing (and growing) and in order to remain competitive, Maintenance Providers must find scalable digital solutions and implement predictive maintenance and prescriptive maintenance together with their customers.
The Impact of Asset Performance Management 4.0
The overarching benefits of APM are abundant. In the APM Maturity Model report, Capgemini measured operational and financial impact on APM. Operationally, companies have been found to reduce their downtime by up to 50%, and experience up to 70% less breakdowns. Financially, companies have been found to reduce their maintenance costs by up to 25% and increase their monthly operational margins by up to 18%. More estimates can be found below:
Throughout our 21 years in business, our customers have experienced similar results – companies ranging from the fields of oil & gas to utility or manufacturing. In this day of total connectivity, Asset Performance Management is one of the main ways to gain a competitive advantage in an ever more challenging industrial environment. Transition to Asset Performance Management 4.0 requires long-term strategic commitment and initial investment. However, if made carefully, such decisions usually pay off in a big way.
If you want to learn more about the Asset Performance Management 4.0 transition, predictive maintenance, and prescriptive maintenance feel free to download our ebook below.
APM Software E-book
Download our e-book to learn what UReason can do for you, find the unique functionalities of our next-gen APM software, look at the big data analytics framework and learn the different asset analysis models.