In some places, turnarounds don’t happen very often. There’s a true story about a supermajor refining company getting ready to do a turnaround, and finding out that there hadn’t been one since before they laid off and allowed early retirement to all of the people who had been responsible for doing the last one. Eventually they hired back as many of their retired and laid off workers as they could, but at consultants’ wages.
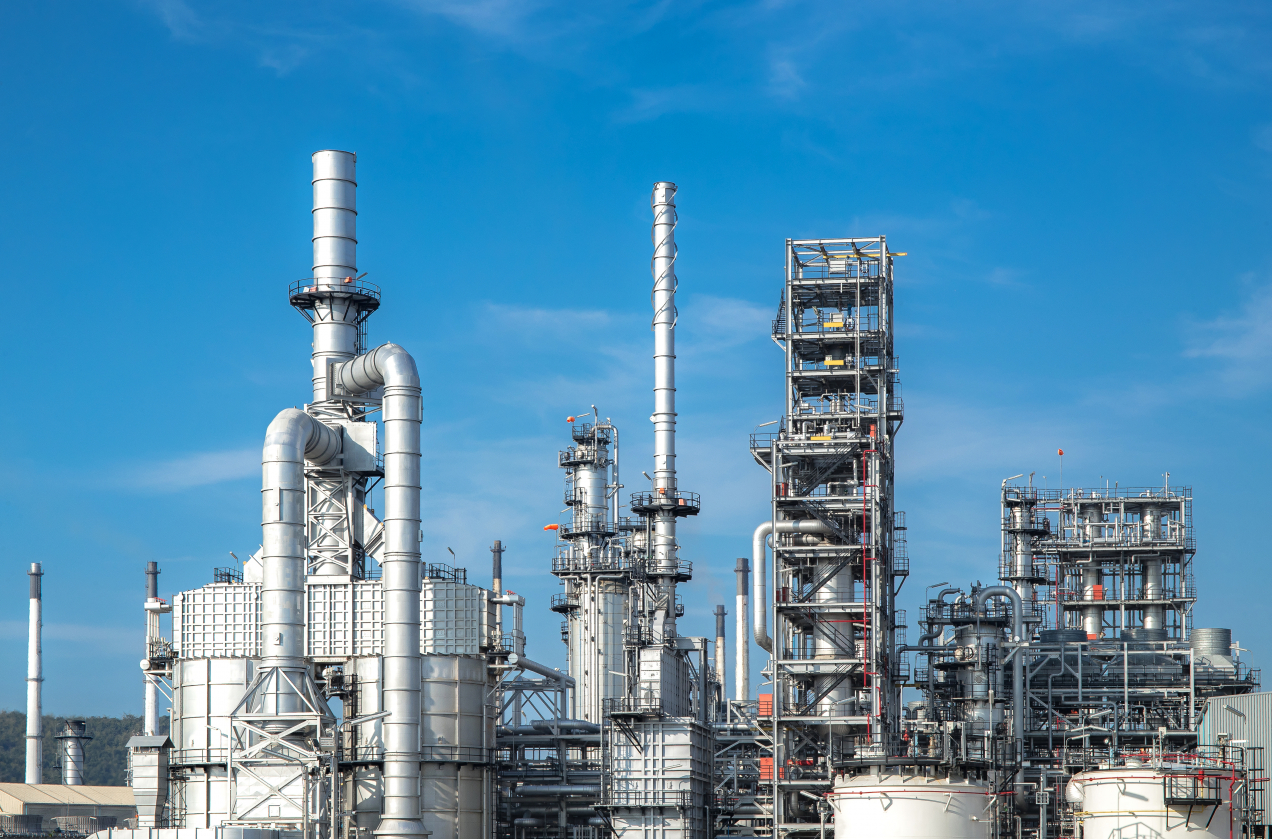
The point of this story is that much of the work of planning and carrying out a turnaround in a refinery or other process plant is more institutional knowledge than following directions from the manuals and as-built drawings. First, manuals and as-builts become obsolete within days or weeks of the plant becoming operational, and are rarely, if ever, updated except by the practice of putting post-it notes on the pages with cryptic comments in bad handwriting. Second, it is the operators and maintenance technicians who know when components are likely to fail. They don’t usually write down what they know, either.
Common knowledge says that control valves and actuators are among the biggest “bad actors” on the plant site, and so they are often scheduled for maintenance during a turnaround. Many companies replace valves and actuators prophylactically (whether they need replacing or not) because they know that replacing them will keep them from failing soon after the turnaround. This doesn’t always help, though, and it is costly to replace a perfectly good valve just because it might fail at a later date.
When replacing valves and actuators, it is also a common failure to install the wrong actuator or the wrong valve trim. It is hard to keep track of these, and it is an inventory nightmare to keep multiple sets of valve trim or even complete valves with different trim installed. If the maintenance techs install the wrong valve trim during turnaround, it is probable that the valve will have premature sudden failure. Sometimes the failure doesn’t exactly come from the valve. In process plants with pneumatic actuators, the failure may be in the air supply. These failures are famously hard to trace, and they can make the actuator fail over and over for undiscoverable reasons.
Shouldn’t the maintenance technicians and operators be able to discover operational data on every valve and actuator? They should, but access to the process or CMMS databases is often restricted to engineering. In addition, very few technicians and operators are data scientists, and therefore their data mining skills are low and lacking. In some plants, operational data is still collected manually, and the piles of paper are kept in the maintenance office closet.
So the question is how do you skip past all that failed history of maintenance faults, and really get a handle on your control valve and actuator problems? Is there a quick, technician and operator-friendly way to figure out which valves and actuators are going to fail soon, and which may never fail?
And please can it be a solution that doesn’t cost an enormous amount and require approval from the Board of Directors?
You can use UReason’s Control Valve App—a simple, stand-alone app that will take the data you already have, and use it in an AI-based analysis engine to tell you which control valves will fail soon and when they fail.
UReason’s Control Valve App (CVA) is based on UReason’s extensive expertise in valves, actuators, and the relevant processes. It uses intelligent models that combine domain knowledge and artificial intelligence (AI) to provide immediate detailed analysis of the process and recommendations for control valves. In the basic app, a PDF report is the output, while the premium version can have an online dashboard and provide job orders in the maintenance management system of the plant.
If you want to see how the CVA works, and how you can best use it, you can download the CVA brochure.
Download Control Valve App brochure
Get more information about how Control Valve App can optimize your valve maintenance and operations