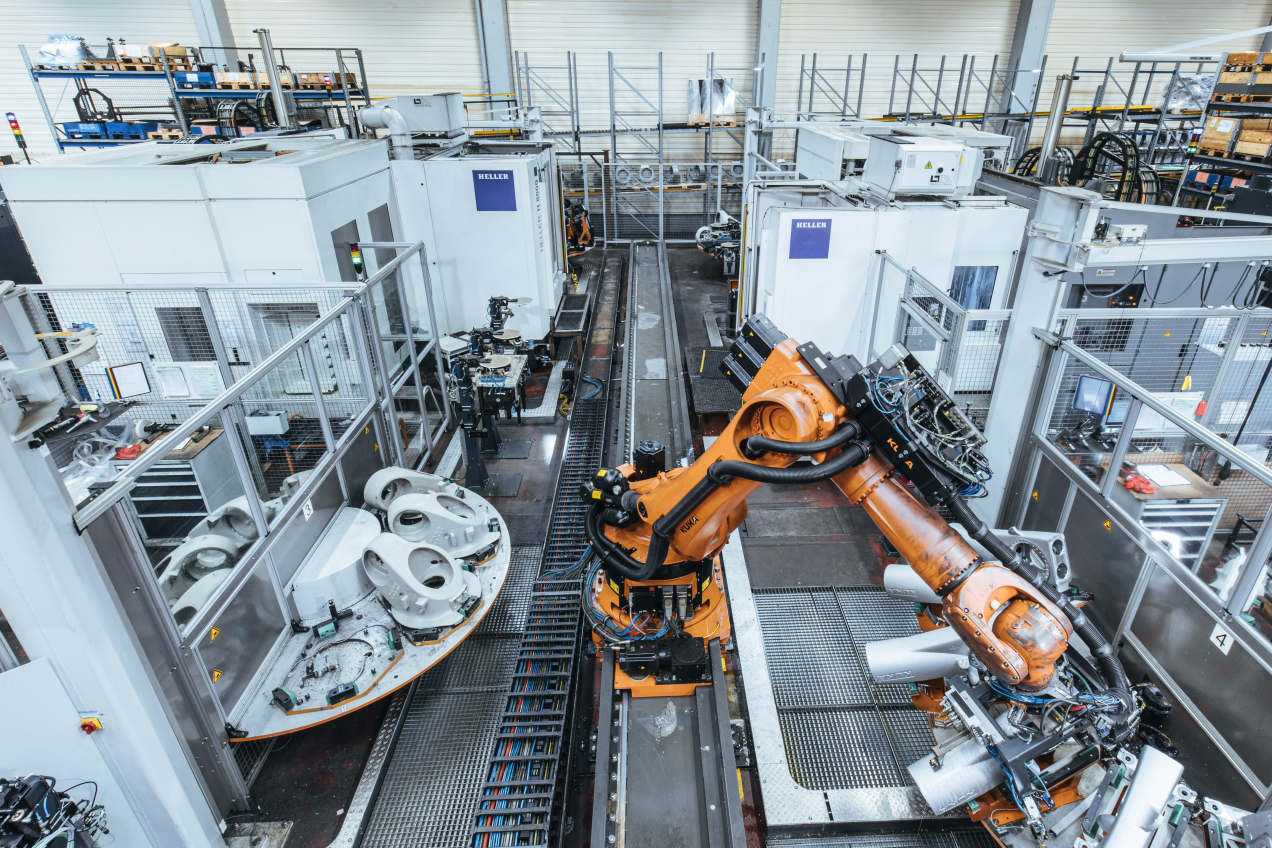
An Intelligent Solution
KUKA runs a fully automated production cell with HELLER Milling Centers at the Augsburg Headquarter site. During the night shifts and weekends, some of the tools may run to the end of its life cycle. This unables production to run until personnel are back on-site.
UReason developed an algorithmic recommender solution within APM Studio that connects to production cell streaming data based on the Open Industry 4.0 alliance reference architecture and guidelines. The recommender system uses the remaining life cycle of the tools, the available parts, and the production programs to advise to shop floor personnel on what specific actions to take regarding tool change to ensure an unmanned production without disruptions.
Benefits for KUKA and the Industry
For KUKA, the APM Studio solution provides production insights and enables them to achieve higher production outputs and efficiency while also minimizing downtime, especially during unmanned production.
The keyword for the future of manufacturing is interoperability, where seamless connectivity with different systems and vendors is a requirement rather than a nice-to-have. With APM Studio, KUKA’s production cell is compatible with the Open Industry 4.0 reference architecture and guidelines, breaking down the barriers to connectivity and bringing the industry closer together for more efficient production.
The Problem
The Heller 8000 has more than 200 individual tools to drill, cut or deburr. There are two turning tables available and a KUKA robot handles the raw and produced parts of the Heller machine.
For a single raw part and program running in the Heller 8000, a certain number of tools are used. Each tool has a dedicated maximum number of parts for which it can be used. Once the tool reaches the pre-warning, an operator can check it for possible additional use or replacement. In the case of unmanned production, if the tool is no longer usable the entire production would come to a stop.
Tool Change Recommender System
To solve this issue, UReason has developed a dashboard that gives personnel an overview of the current status of the tools in the Heller 8000. This overview supports the production process.
Additionally, a recommender has been set up that calculates, based on the requirements of maximum unmanned production, which tools need to be inspected/changed. This ensures that personnel has a quick overview of the required actions to perform the current or maximal production without any tooling issues. Furthermore, an automated report is generated daily and sent to the supervisors via the preferred communication channels. This way, supervisors have a detailed overview of the situation in the production cells on a daily basis.
The recommender tool acts as an automated decision-making application that makes the management and optimization of the production cell more transparent and autonomous.
Learn More About This Solution
Want to know more about APM Studio and how it can support your production?